
Power Optimization of Electro Thermal Systems Project
The scientific process is comprised of numerous components, many of which greatly affect our ability to actually conduct experiments and verify their results. Uncertainty is arguably one of the most important. Almost every field in research utilizes uncertainty theory to some degree, heat transfer is no exception. Our goal in this project was to assist PhD Candidate Ki Wook Jung’s 3-D Manifold Heat Sink experiment by determining the uncertainty of a heat exchanger’s heat transfer coefficient in the experiment flow loop. In this experience I gave a solo presentation to the nanoHeat research group related to my interests in Tesla thermal management systems, and Tesla's new patents for battery pack technology. The rest of the internship was partnered with Quinton Williams (Nuclear Engineer) and we pretty much were together doing everything throughout the experience, thus we both equally worked in the lab and on all aspects of the project.
POETS

Overview of POETS
The high level goal of the POETS's organization is to co-design thermal regulation systems with electrical power to achieve increased power density across a broad array of industrial and consumer uses. The project we were working on at Stanford was in enabling technology in the thrust 2, which consists of multi-disciplinary design tools that enhance the ability to create new physical architectures, then determines how best to operate these as-designed systems. Specifically a 3-D manifold heat sink, designed to the thermally regulate 5mm x 5mm hot spot for high heat flux chips.

3-D Manifold Heat Sink
Essentially this 3D manifold uses embedded cooling  semiconductor, instead of a traditional heat sink's that have indirect cooling, meaning the liquid is passed through a heat sink with a thermal interface material sandwiched between the heat sink and the semiconductor device. Thus the total thermal resistance adds up and bottle necks the ability to move more heat away from the semiconductor device. Using embedded cooling is a direct method that can eliminate most of these resistances as it directly cools the semiconductor device closest to the heat source. The PhD Students at Stanford were working on this project for a couple years prior to us coming in for our internship, but it was very interesting to see how this device works, and to help them work on testing it. They were really concerned with minimizing pressure drop through the test section will maximizing heat flux to have the best possible performance out of the device.

Flow Concept of 3-D Manifold
This is the concept design of an in-chip embedded microchannel-3D manifold cooler. Essentially the working fluid, water, enters from the top left and right, takes a 90 degree turn upwards and then a 180 degree turn down words towards the outlets. The blue to orange color change signifies how the heat enters the fluid as it cycles through the micro-channels taking heat away from the semiconductor chip.
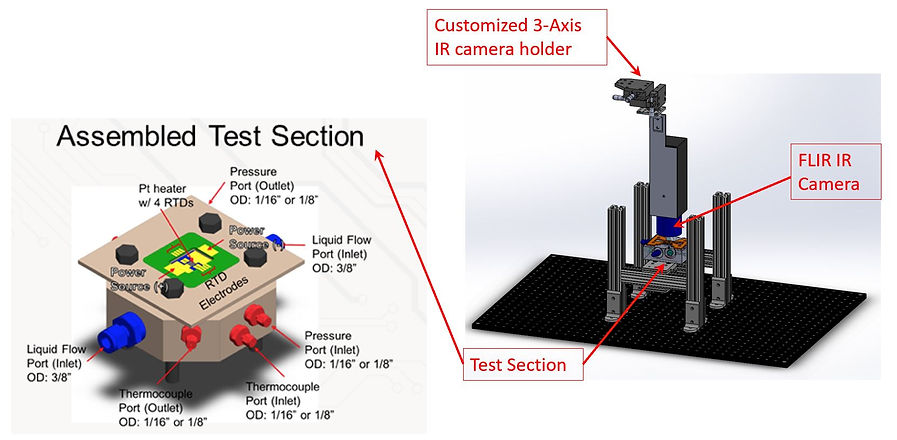
Test Section
The test section and the flow loop the working fluid must go through before entering the manifold is really important for conducting analysis on this device. As you can see on the left, the assembled test section, it was important to monitor the temperature and pressure of the working fluid at the inlet and the outlet of the microchannel manifold. And the semiconductor device needs to be simulated, therefore there is a controlled heating source that must be powered and temperature must be monitored with RTD's (Resistive Temperature Detector) to understand how much heat is experimentally being transferred. Also to the right you can see how the test section sits on the 8020 aluminum frame with IR camera to detect changes in temperature using inferred waves projected off the hot spot.

Schematic
The flow loop is pretty complex because the fluid is entering in microchannels on the manifold, thus it is important to regulate and montitor the flow into the device. Thus you can see after the micro pump, there is a micromotion mass flow meter and a pre heater before going into the test section, this will ensure closed loop control of the flow going into the test region. As the fluid comes out of the test section it is hot and must be cooled by going into a cross flow heat exchanger which is labeled as the condenser in the schematic. We never used the accumulator so I am completely unsure what kind of tests there doing with that, but I would assume they would build pressure in there to be used as work input and bypass the micropump in that configuration.
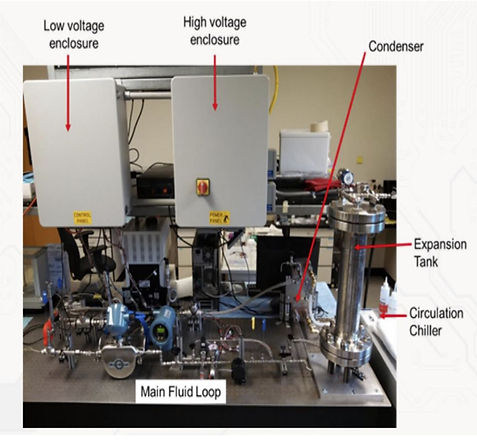
Lab Hardware
This is just a picture of all the hardware within the lab that was used during testing, and replicates everything depicted within the above schematic.

Finding Heat Transfer Coefficient
As interns we were tasked with finding the heat transfer coefficient experimentally for the cross flow heat exchanger that takes the heat out of the loop via the NESLAB THERMOFLEX 3500 CHILLER. This task required taking data of the temperatures and pressures of all 4 locations, inlet & outlet of the working fluid of the loop, and inlet & outlet of the chiller itself. Then we were tasked with calibrating and finding the uncertainty of all the thermocouples within the loop.

Thermocouple Calibration Method
For the thermocouple calibration, we used a much more precise thermometer, and a water bath that would maintain a specific temperature as depicted above. This took a while to do as it took a lot of time for the water temperature to reach steady state within the bath, and there were a lot of thermocouples that needed to be calibrated between the temperatures 25 to 100 degrees Celsius. The heat exchanger in the picture is only holding the foam insulation in place and is just essentially a weight.

Thermocouple Calibration Results
As you can see from the results, the Thermocouple calibration was successful in reducing the uncertainty. The graph is representing the highly precise probe temperature on the y-axis and the actual thermocouple temperature on the x-axis thus creating a linear fit capture the bias of each thermocouple and improve the current uncertainty of each plus or minus 1 degree Celsius to the values captured in the table to the right. As you can see it is almost an order of magnitude of improvement thus really worth doing.

POETS National Conference in Illinois
Apart of the experience was to fly out to Illinois to go to the POETS national conference at the University of Illinois Urbana-Champagne. It was the first time ever for me to go on a plane and it was a really great experience to go there and meet so many awesome people from all over the country!